Préparation de l'air dans les systèmes pneumatiques
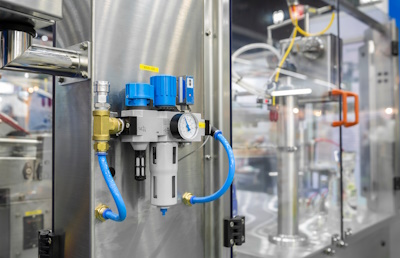
Figure 1 : Filtre régulateur lubrificateur d'air comprimé
L'air comprimé dans les systèmes pneumatiques contient souvent de l'humidité et des contaminants et peut être à une pression inadaptée pour une utilisation directe, endommageant potentiellement l'équipement en aval. Pour conditionner l'air, il passe à travers des filtres, des régulateurs et des lubrificateurs, qui le nettoient et ajustent la pression. Cet article examine les composants de la préparation de l'air, leurs fonctions et critères de sélection.
Table des matières
- Préparation de l'air comprimé dans un système pneumatique
- Particules dans l'air comprimé et leurs conséquences
- Unités de préparation de l'air dans un système pneumatique
- Comment choisir la bonne unité de préparation de l'air
Consultez notre sélection en ligne de FRL et de silencieux pneumatiques !
Préparation de l'air comprimé dans un système pneumatique
L'air comprimé est de l'air maintenu à une pression supérieure au niveau atmosphérique. C'est une source d'énergie vitale dans les systèmes pneumatiques pour diverses applications industrielles. La préparation de l'air comprimé commence avec l'air ambiant (Figure 2 étiquetée A), qui est aspiré dans un compresseur (Figure 2 étiquetée B) qui le met sous pression et l'envoie à un réservoir (Figure 2 étiquetée C) pour le stockage. Pour garantir que l'air est propre et sec, il passe à travers un sécheur frigorifique (Figure 2 étiquetée D) qui élimine l'humidité. Ensuite, il passe à travers des composants de préparation de l'air (Figure 2 étiquetée E) pour éliminer les impuretés et maintenir une pression suffisante (discuté plus tard). Finalement, l'air préparé est fourni à la machine (Figure 2 étiquetée F) à travers des tuyaux.
L'air comprimé traverse divers dispositifs, tuyaux et raccords qui peuvent introduire des contaminants. Une préparation supplémentaire de l'air au point d'utilisation est essentielle, surtout sur de longues distances ou dans des environnements sujets à l'accumulation d'humidité et de particules.
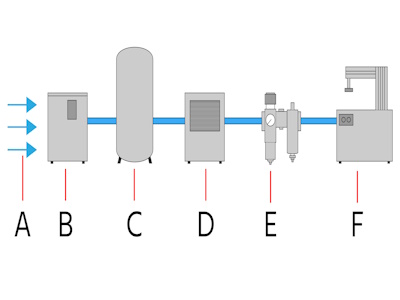
Figure 2 : Composants du système de préparation de l'air pneumatique : air ambiant (A), compresseur (B), réservoir (C), sécheur frigorifique (D), préparation de l'air (E) et machine (F).
Particules dans l'air comprimé et leurs conséquences
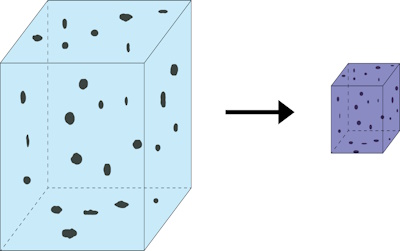
Figure 3 : La concentration des contaminants augmente considérablement lorsque l'air est comprimé
Un mètre cube d'air de l'environnement contient de nombreux composants susceptibles de poser des problèmes dans les systèmes pneumatiques. Ceux-ci incluent :
- Particules de saleté : Les particules de saleté pourraient être aussi nombreuses que 180 millions de particules allant de 0,01 micromètres à 100 micromètres de taille.
- Eau : La quantité d'eau varie avec la température, mais à 50 𐩑C, il peut y avoir environ 80 grammes d'eau.
- Huile : Il peut y avoir jusqu'à 0,03 milligrammes d'huile.
- Contaminants chimiques : Les contaminants chimiques incluent des substances nocives comme le plomb, le cadmium, le fer, le mercure et d'autres.
Le tableau 1 discute des conséquences de ces particules dans l'air comprimé. Nettoyer l'air comprimé est crucial pour prévenir les dommages et assurer le fonctionnement en douceur des composants. De plus, différentes industries et applications spécialisées peuvent avoir leurs normes pour la propreté de l'air comprimé.
Tableau 1 : Les particules dans l'air comprimé et leurs conséquences
Particules | Conséquences directes | Conséquences à long terme |
Particules solides : Particules solides telles que la poussière, les écailles de rouille ou les copeaux de métal créés pendant la fabrication ou d'autres processus. | Accumulation et usure des pièces frottant les unes contre les autres, par exemple, entre la paroi du cylindre et le joint sur le piston. |
|
Eau : L'air atmosphérique contient toujours une certaine humidité. | Rouille des composants créant des particules de rouille pouvant entraîner des dommages mécaniques ou obstruer les passages étroits par lesquels passent les fluides. | |
Huile : Même dans les compresseurs qui n'utilisent pas d'huile, de minuscules gouttelettes d'huile de l'air aspiré peuvent laisser des traces de contamination par l'huile. | Agglomération des particules menant à des sections bloquées. De plus, l'huile peut faire gonfler les élastomères, tels que ceux dans les joints. |
Unités de préparation de l'air dans un système pneumatique
Les unités de préparation de l'air font généralement référence aux divers composants installés le long du système pour préparer et maintenir la qualité de l'air comprimé avant qu'il n'atteigne le point d'utilisation. Les principales unités sont discutées ci-dessous.
FRL
Une unité FRL est un système de conditionnement d'air comprimé modulaire composé d'un filtre, d'un régulateur et d'un lubrificateur, conçu pour éliminer les contaminants, ajuster la pression et ajouter du lubrifiant à l'air comprimé dans les systèmes pneumatiques. Bien que ces composants soient souvent intégrés dans un seul système, ils peuvent également être trouvés en tant qu'unités séparées, telles qu'un régulateur seul ou un régulateur de filtre combiné. Les systèmes pneumatiques modernes, équipés de composants auto-lubrifiants, n'ont souvent pas besoin de lubrificateurs.
Filtre
Un filtre élimine les contaminants tels que la poussière, la vapeur d'eau et l'huile présents dans l'air comprimé. Dans certains systèmes, plusieurs filtres sont nécessaires en raison de divers besoins :
- Le système doit éliminer les contaminants des tuyaux ou la condensation qui se produit pendant le transit avant que l'air n'atteigne chaque équipement.
- Différents dispositifs de contrôle ou de régulation nécessitent de l'air à différents niveaux de propreté.
- Certaines applications, comme l'emballage alimentaire, exigent plus qu'une filtration standard. Ici, des filtres à charbon actif sont nécessaires ; l'air doit passer à travers des filtres fins avant de les atteindre.
Les systèmes pneumatiques utilisent généralement des éléments filtrants capables de capturer des particules entre 5 et 50 micromètres (µm) de taille. Pour atteindre une qualité d'air qui répond à la norme ISO 8573-1:2010 [7:4:4], les critères suivants doivent être respectés :
- Concentration de particules : 5-10 milligrammes par mètre cube (mg/m³)
- Finesse du filtre : 20-50 µm
Pour des normes plus élevées, la conception doit adhérer à la spécification ISO 8573-1:2010 [6:4:4] :
- Concentration de particules : Pas plus de 5 mg/m³
- Finesse du filtre : 5 µm
Les éléments filtrants doivent être remplacés régulièrement car ils se bouchent avec des polluants au fil du temps, conduisant à une réduction du débit d'air. Une chute de pression d'air peut être identifiée en mesurant la différence de pression avant et après le filtre. À mesure qu'un élément filtrant se salit, la chute de pression à travers le filtre augmente (typiquement égale ou légèrement inférieure à 0,5 bar), indiquant le niveau de blocage de l'élément filtrant.
Régulateur
Un régulateur de pression gère la pression de l'air comprimé dans un système pneumatique, assurant que l'équipement en aval reçoit de l'air à la pression correcte. Le réseau fournit typiquement une pression allant de 6 à 10 bars, qui peut fluctuer en fonction de la quantité d'air utilisée. Pour utiliser efficacement l'air comprimé, chaque pièce d'équipement devrait avoir sa pression nécessaire réglée à l'aide d'un régulateur de pression séparé.
Lubrificateur
Un lubrificateur ajoute des quantités précises d'huile dans le flux d'air comprimé. Les fabricants de composants mécaniques visent à créer des produits qui n'ont pas besoin de lubrification supplémentaire. Cela est réalisé en utilisant des matériaux appropriés, en sélectionnant les bons systèmes d'étanchéité, en minimisant la friction ou en fournissant au produit une lubrification permanente suffisante au moment de l'achat. Des graisses spéciales sont fabriquées à cet effet, destinées à rester indéfiniment dans les vannes ou les cylindres. Pour éviter que le lubrifiant ne soit emporté, il est important d'utiliser de l'air sec, car l'humidité peut endommager le lubrifiant. Cet effet de lavage se produit également avec les lubrificateurs, il est donc crucial de s'assurer que les lubrificateurs ne manquent jamais de lubrifiant.
Silencieux pneumatique
Un silencieux pneumatique est un dispositif attaché au port d'échappement d'un composant du système pneumatique, tel qu'une vanne ou un cylindre, pour réduire le bruit créé par l'air comprimé s'échappant. Il fonctionne en permettant à l'air de se dilater et de ralentir avant d'être libéré dans l'atmosphère, ce qui diminue le niveau de bruit. Certains silencieux peuvent également piéger ou filtrer les contaminants de l'air d'échappement.
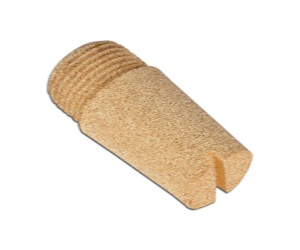
Figure 4 : Silencieux pneumatique
Refroidisseurs d'après
Les refroidisseurs d'après refroidissent l'air après qu'il a été comprimé et avant qu'il n'entre dans le sécheur d'air, ce qui aide à éliminer l'humidité.
Sécheurs d'air
Les refroidisseurs d'après peuvent éliminer environ 85 % de l'humidité de l'air d'un compresseur. Pour éliminer encore plus d'humidité, des sécheurs d'air sont utilisés après les refroidisseurs d'après, surtout quand il est important de garder l'air de devenir trop humide lorsqu'il circule dans le système pneumatique. Cela est crucial dans les applications nécessitant de l'air très sec, comme dans les processus sensibles à l'humidité, pour prévenir la corrosion ou pour assurer le bon fonctionnement de l'équipement pneumatique.
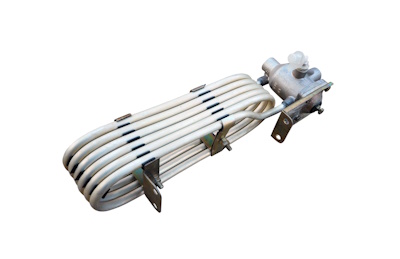
Figure 5 : Sécheur d'air pour système pneumatique
Drains
Les drains éliminent tout condensat accumulé de divers points dans le système pneumatique, en particulier du récepteur d'air et des filtres.
Comment choisir la bonne unité de préparation de l'air
La préparation adéquate de l'air pour un dispositif utilisant de l'air comprimé implique trois facteurs principaux :
- Pureté de l'air comprimé
- Débit adéquat
- Pression de travail optimale
Pureté de l'air comprimé appropriée
L'air propre aide le système pneumatique à durer plus longtemps et à fonctionner efficacement, et il répond aux règles pour certaines industries, comme la production alimentaire. La norme ISO 8573-1:2010 définit la pureté de l'air comprimé.
- La classe de pureté est déterminée par trois facteurs - particules solides, eau et huile.
- Pour chaque catégorie de ces contaminants, la norme spécifie la quantité maximale de contamination autorisée dans l'air comprimé.
Plus le numéro de classe est élevé, moins l'air doit être pur. Les fabricants de composants pneumatiques comme les vannes et les cylindres donnent le niveau de pureté de l'air nécessaire pour que leur équipement fonctionne correctement. Différentes applications nécessitent différents niveaux d'air comprimé propre pour bien fonctionner.
Par exemple, si un système pneumatique spécifie une exigence de qualité de l'air comprimé comme 'Classe 2.4.1', cela signifie :
- Pour les particules solides (premier chiffre), Classe 2 : L'air ne doit pas contenir plus de 100 000 particules/m³ de taille ≥ 1 micron, 1 000 particules/m³ de taille ≥ 5 microns, et 10 particules/m³ de taille ≥ 10 microns.
- Pour l'eau (deuxième chiffre), Classe 4 : L'air doit avoir un point de rosée sous pression ne dépassant pas +3 °C, ce qui limite la quantité de vapeur d'eau pouvant se condenser en eau liquide à une pression donnée.
- Pour l'huile (troisième chiffre), Classe 1 : L'air ne doit pas contenir plus de 0,01 mg/m³ d'huile.
Débit adéquat
Des débits adéquats sont nécessaires pour assurer un fonctionnement correct et la vitesse des composants, par exemple, pour garantir que les pistons des cylindres se déplacent aux vitesses supposées.
Le débit est principalement décidé par la taille des ouvertures dans les pièces et leur conception. Si les pièces sont conçues de manière similaire, les plus grandes permettront un plus grand flux d'air. Cependant, le débit peut changer en fonction de l'application de ces pièces. Par exemple, les filtres résistent naturellement au flux d'air et peuvent réduire le débit.
Des problèmes tels que les restrictions de débit, les fuites et les longs trajets de tuyauterie peuvent causer des pertes de pression significatives. Pour minimiser cela, il est recommandé de maintenir une pression d'entrée au système de préparation de l'air de la machine qui est de 10 à 20 % supérieure à la pression de fonctionnement et d'envisager d'augmenter la taille des tuyaux d'alimentation si nécessaire.
Si les bonnes pièces sont choisies pour le travail, mais que le système n'obtient toujours pas un débit d'air suffisant, vérifiez les facteurs suivants :
- Les points de connexion pour l'alimentation en air sont-ils sous-dimensionnés ?
- Y a-t-il des problèmes causés par les longues conduites d'air, ayant trop de branches, ou des courbures serrées ?
- Les surfaces intérieures des conduites d'air sont-elles rugueuses ou sales ?
- Y a-t-il des fuites non détectées dans le système ?
La bonne pression de fonctionnement
La pression de fonctionnement doit correspondre à la pression nécessaire pour déplacer les pièces pneumatiques. Une pression appropriée assure que le système a assez de puissance pour fonctionner.
Chaque dispositif utilisant de l'air comprimé est conçu pour fonctionner au mieux dans une plage de pression spécifique. Si la pression est trop basse, le système ne fonctionnera pas aussi bien qu'il le devrait. Si la pression est trop élevée, cela peut causer une usure plus rapide des pièces comme les joints, consommer plus d'énergie et faire beaucoup de bruit. Il est donc important de considérer les chutes de pression possibles lors de la détermination de la bonne pression. Ces chutes de pression peuvent se produire en raison de :
- Des dispositifs utilisant l'air, comme les vannes, les filtres et les sécheurs.
- Des longs tuyaux, des branches, des courbures trop serrées, des surfaces intérieures rugueuses et de la saleté dans les tuyaux.
- Des fuites non détectées.
La pression maximale d'un élément pneumatique dépend de plusieurs paramètres, comme le matériel du boîtier et les ressorts utilisés pour l'ajustement.