Capteurs de vérins pneumatiques - Leur fonctionnement
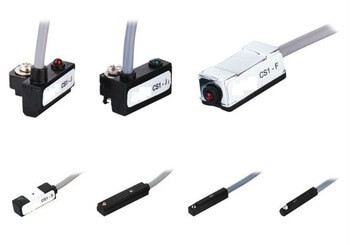
Figure 1 : Différents capteurs de proximité pour vérins pneumatiques
Les capteurs sont essentiels pour fournir des retours de position aux systèmes de contrôle dans les machines et équipements automatisés. Dans les cylindres pneumatiques, les capteurs sont utilisés pour détecter la position linéaire du piston, ce qui est crucial pour les applications nécessitant un retour de position précis. Les capteurs les plus courants pour les cylindres pneumatiques sont les capteurs de proximité magnétiques, qui détectent le champ magnétique d'un aimant intégré dans le piston du cylindre. Ces capteurs sont montés sur le corps du cylindre pneumatique et indiquent "ON" ou "OFF" en fonction de leur proximité avec l'aimant. Selon l'application spécifique, diverses technologies de capteurs de proximité magnétiques peuvent être utilisées pour optimiser les performances, l'espace et la fiabilité. La figure 1 illustre des exemples de différents capteurs de proximité pour cylindres pneumatiques.
Les capteurs Reed sont le type le plus courant de capteurs pour vérins pneumatiques. Ils sont utilisés depuis des années et constituent une technologie éprouvée. Les deux principaux motifs de préoccupation pour un capteur à lames par rapport à d'autres capteurs examinés ci-dessous sont la durée de vie et les chocs/vibrations. Les capteurs Reed ont généralement un cycle de vie de plus de 10 millions d'années et le capteur Reed n'est généralement pas le premier à tomber en panne lorsqu'il est soumis à des chocs ou à des vibrations importants. Pour ces raisons, les capteurs à lames ont été et sont toujours les capteurs les plus populaires pour les vérins pneumatiques.
Consultez notre sélection en ligne de capteurs pour vérins pneumatiques !
Table des matières
- Pourquoi utiliser un capteur pour un vérin pneumatique ?
- Montage du capteur de vérin pneumatique
- Options de capteurs de proximité magnétique
- Comment choisir entre les capteurs ?
- Comparaison des capteurs de vérins pneumatiques
- Acheter des capteurs de position en ligne
Pourquoi utiliser un capteur pour un vérin pneumatique ?
Les capteurs de position linéaire de vérins pneumatiques sont utilisés pour détecter la position linéaire du piston pendant le fonctionnement. Les cylindres pneumatiques sont généralement fabriqués avec un aimant déjà fixé à l'intérieur du piston, ce qui permet d'utiliser des capteurs de proximité magnétiques si nécessaire. Selon l'endroit où le capteur est monté, il peut détecter une extension, une rétraction ou des positions individuelles le long du corps du vérin. Il est également possible de fixer plusieurs capteurs sur un cylindre pneumatique pour obtenir plusieurs emplacements de retour de position. Les vérins pneumatiques équipés de capteurs de position offrent une sécurité accrue et un retour d'information permettant de s'assurer de la position du piston pour les applications cruciales.
Montage du capteur de vérin pneumatique
Les deux types de corps de vérins pneumatiques les plus courants sont le profilé, comme ISO 15552, ou le rond, comme ISO 6432. Selon le type de corps, il existe différentes méthodes de montage. Les méthodes de montage peuvent également varier en fonction du type de capteur, il est donc important de comprendre le type de corps de cylindre que vous avez avec le type de capteur.
Cylindres profilés
Les cylindres profilés sont de forme rectangulaire et disposent de deux méthodes simples pour monter les capteurs sur le corps du cylindre. Pour les cylindres pneumatiques conformes à la norme ISO 15552, le corps comporte des rainures permettant d'insérer un capteur, comme le montre la figure 2. Le capteur (1) est ensuite fixé à l'aide d'une vis de réglage (2) à l'aide d'un tournevis (3). D'autres cylindres profilés sont équipés de tirants, qui s'étendent sur toute la longueur du corps du cylindre aux quatre coins. Les capteurs peuvent être montés sur le tirant et glissés dans la position appropriée sur la longueur du cylindre.
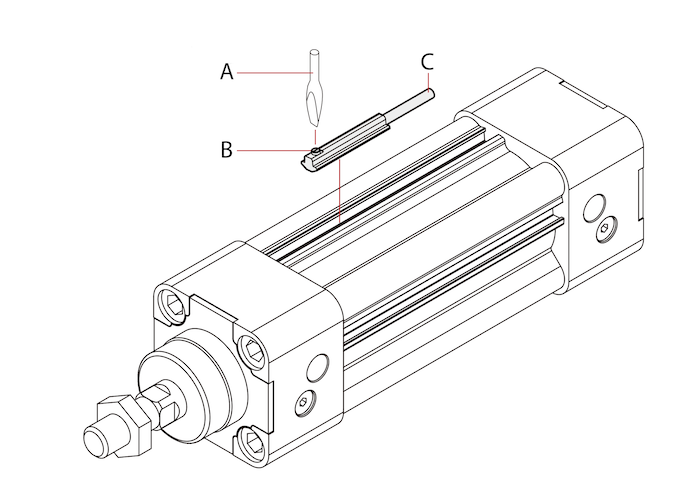
Figure 2 : Vérin pneumatique ISO 15552 avec un capteur (C) monté via la vis de réglage (B) avec un tournevis (A)
Cylindres ronds
Les cylindres ronds sont généralement plus petits, comme l'ISO 6432, mais il est toujours possible d'y monter des capteurs en utilisant une bande circulaire autour du boîtier du cylindre. La bande doit être spécifiée en fonction du diamètre du cylindre. Une fois montés, le capteur et la bande peuvent glisser sur la longueur du cylindre, puis être fixés en place. La figure 3 montre un cylindre pneumatique ISO 6432 sur lequel est monté un capteur.
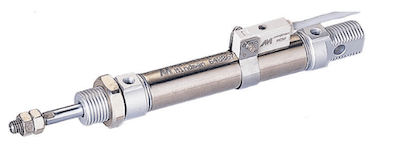
Figure 3 : Vérin pneumatique ISO 6432 avec capteur monté
Options de capteurs de proximité magnétique
Tous les capteurs utilisés pour les vérins pneumatiques afin d'obtenir un retour d'information sur la position linéaire du piston utilisent un champ magnétique. C'est pourquoi tous les vérins pneumatiques sont déjà équipés d'un aimant situé à l'intérieur du piston. Cependant, il est toujours important de vérifier cette spécification de conception pour votre vérin pneumatique si un retour de position linéaire est nécessaire.
Interrupteur à lames
Un capteur à lames est un capteur de proximité magnétique qui est activé lorsqu'un champ magnétique aligné axialement lui est appliqué. Les pôles magnétiques d'un aimant aligné dans l'axe sont proches les uns des autres dans le plan axial. Lorsque l'aimant aligné axialement s'approche du capteur à lames, un champ magnétique parallèle à l'interrupteur à lames est généré. Un interrupteur à lames est composé d'une paire de lames métalliques ferromagnétiques, qui sont enfermées dans un tube de verre scellé. En l'absence de champ magnétique (image du haut, figure 4), les peignes métalliques se séparent et le capteur s'éteint. Lorsque le piston du cylindre passe devant le commutateur et applique un champ magnétique suffisamment puissant pour attirer les peignes ensemble (image du milieu, figure 4), le capteur est mis en marche (image du bas, figure 4).
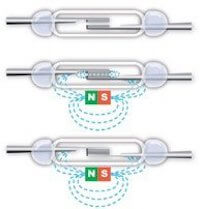
Figure 4 : Fonctionnement de l'interrupteur Reed
Par rapport à d'autres options de capteurs, les interrupteurs à lames sont rentables et peuvent fonctionner avec des tensions alternatives ou continues. En outre, les capteurs à lames ont une faible consommation d'énergie, ce qui les rend adaptés aux applications exigeant une consommation d'énergie. En raison de la nature mécanique des contacts à lames, les capteurs à lames ont des limites. Tout d'abord, les contacts de commutation ont un nombre fini de cycles de commutation et devront être entretenus pendant toute la durée de vie de la machine. Ensuite, les capteurs à lames ne conviennent pas aux applications exposées à de fortes vibrations ou à des chocs. Les chocs et les vibrations importants peuvent provoquer le claquement des contacts Reed, ce qui entraîne une signalisation imprécise. Les caractéristiques de commutation d'un interrupteur à lames peuvent également provoquer une double commutation involontaire. On parle de double commutation lorsque la sortie du capteur commute deux fois sur "ON" et "OFF" alors que l'aimant du cylindre passe une fois devant l'interrupteur à lames. La fausse double commutation de la sortie du capteur est due à la force non uniforme du champ de force d'un aimant. L'intensité d'un champ magnétique est la plus forte à chaque pôle de l'aimant et la plus faible au centre entre chaque pôle. Si l'aimant du piston n'est pas assez puissant, il peut provoquer une double commutation de la sortie de l'interrupteur lorsqu'il traverse le capteur. Enfin, par rapport aux capteurs à semi-conducteurs, les interrupteurs à lames sont relativement lents à activer, ce qui les rend inadaptés aux applications nécessitant des temps de réponse rapides. Cependant, les capteurs à lames pour les vérins pneumatiques sont largement utilisés car ils sont relativement peu coûteux par rapport à d'autres capteurs, ne nécessitent pas d'alimentation de secours, peuvent fonctionner avec des charges en courant continu ou alternatif, et constituent une solution connue et éprouvée.
Capteur à effet Hall
Un capteur à effet Hall est un capteur de proximité magnétique qui est activé lorsqu'un champ magnétique aligné radialement lui est appliqué. Un aimant aligné radialement produira un champ magnétique perpendiculaire au champ magnétique du capteur à effet Hall, comme le montre la figure 5. Contrairement aux interrupteurs à lames, les capteurs à effet Hall sont des dispositifs à l'état solide et sont conçus avec des composants différents. Les interrupteurs Reed dépendent de contacts mécaniques mobiles pour fournir une sortie de capteur. Les dispositifs à semi-conducteurs fournissent une sortie de capteur en utilisant des circuits électriques sans composants mobiles. Un capteur à effet Hall est constitué d'un semi-conducteur traversé par un courant continu, comme le montre l'image du haut de la figure 5. Lorsqu'un champ magnétique est appliqué radialement (2) au flux de courant (1), comme le montre l'image du bas de la figure 5, les électrons chargés se séparent sur les côtés opposés du semi-conducteur en fonction de leur polarité. La séparation des électrons chargés induit une tension dans le circuit à effet Hall (4). Lorsque la tension de sortie du circuit est supérieure au seuil de commutation, la sortie du capteur est activée, comme le montre la figure 5.
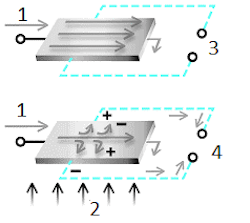
Figure 5 : Fonctionnement du capteur à effet Hall : flux de courant (1), champ magnétique (2), tension = 0 (3 & 4)
Contrairement aux capteurs à lames, les capteurs à effet Hall ne comportent pas de composants mobiles et leur encombrement est plus faible. La conception à semi-conducteurs augmente la durée de vie du capteur grâce à son fonctionnement sans usure et le rend résistant aux chocs et aux vibrations. Sans avoir à surmonter l'inertie des composants mécaniques, les capteurs à effet Hall conviennent également aux applications critiques qui nécessitent une commutation rapide. Comme pour les détecteurs à interrupteur à lames, l'orientation de l'aimant est importante pour un fonctionnement correct. En outre, les capteurs à effet Hall sont peu sensibles. En fonction du diamètre et de l'épaisseur du corps du cylindre, la sortie de commutation peut ne pas s'activer correctement. Comme pour les interrupteurs à lames, les points de commutation doubles sont également possibles en raison de la faible sensibilité des capteurs.
Capteur magnétorésistif anisotrope
Un capteur magnétorésistif anisotrope (AMR) est un capteur de proximité magnétique à l'état solide qui est activé lorsqu'un champ magnétique radial ou axial lui est appliqué. Un circuit AMR se compose d'un pont de Wheatstone (figure 6) pour mesurer la résistance. La résistance d'un capteur AMR diminue avec l'intensité du champ magnétique, ce qui se traduit par un gradient de tension plus important dans le circuit AMR. Lorsque la tension dans le circuit est supérieure au seuil de commutation (figure 6, point 3), la sortie du capteur est activée, comme le montre la figure 6, point 4.
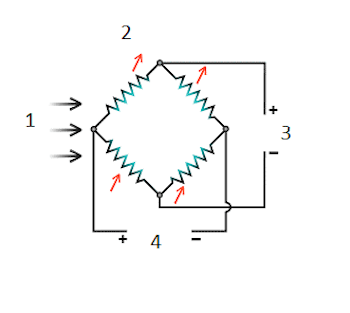
Figure 6 : Fonctionnement du capteur AMR : champ magnétique (1), champ magnétique appliqué (2), tension de polarisation (3) et tension = 0 (4)
Comme les capteurs à effet Hall, les capteurs AMR agissent rapidement, ne s'usent pas et résistent aux chocs et aux vibrations. L'avantage des capteurs AMR est qu'ils sont moins sensibles que les capteurs à effet Hall et qu'ils réagissent bien aux variations de l'intensité du champ magnétique. Il en résulte une meilleure détection des pistons sur de plus grandes distances grâce à sa capacité à détecter des champs magnétiques plus faibles. La possibilité d'avoir des points de commutation doubles est éliminée en raison de la sensibilité plus élevée. En outre, les capteurs détectent les aimants magnétisés axialement et radialement. Les détecteurs AMR sont plus compacts que les détecteurs à interrupteur à lames et leur coût est compétitif. L'inconvénient des capteurs AMR est qu'ils consomment généralement du courant en permanence. Pour les applications nécessitant une faible consommation d'énergie, un capteur à interrupteur à lames peut s'avérer plus approprié.
Capteur magnétorésistif géant
Un capteur magnétorésistif géant (GMR) est un capteur de proximité magnétique à l'état solide qui est activé lorsqu'un champ magnétique radial ou axial lui est appliqué. Un capteur GMR est composé de différentes couches de conducteurs magnétiques et non magnétiques alternés, comme le montre la figure 7, numéros 2 et 3. Comme pour un capteur AMR, lorsqu'un champ magnétique est appliqué au capteur, les propriétés de résistance du circuit changent, ce qui crée un gradient de tension plus élevé à travers le circuit à mesure que le champ magnétique augmente. Par exemple, en présence d'un champ magnétique (figure 7 numéro 1), la résistance du circuit diminue, ce qui permet au courant de circuler (figure 7 numéro 4) et à la tension à travers le circuit d'augmenter. Lorsque la tension à travers le circuit est supérieure au seuil de commutation, la sortie du capteur est activée.
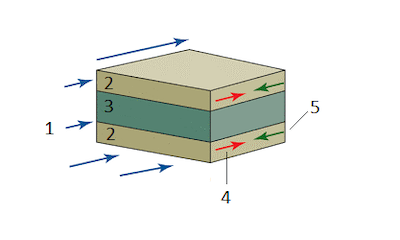
Figure 7 : Fonctionnement du capteur GMR : champ magnétique externe appliqué (1), couche ferromagnétique (2), couche non magnétique conductrice (3), faible résistance avec champ magnétique appliqué (4) et forte résistance sans champ magnétique externe (5).
Les capteurs GMR offrent les mêmes avantages que les capteurs AMR, mais ils sont encore plus sensibles à la présence d'un champ magnétique. La sensibilité élevée permet également d'obtenir un capteur très compact, qui convient aux cylindres plus petits et plus courts. Bien que la sensibilité élevée soit un avantage pour les applications qui nécessitent un retour d'information immédiat du capteur, elle peut provoquer des signaux de sortie non intentionnels si elle est perturbée par des champs magnétiques environnants. Par exemple, les environnements avec une forte puissance à proximité (moteurs CA ou alimentation CA) peuvent perturber le signal du capteur et provoquer des erreurs involontaires.
Comment choisir entre les capteurs ?
Pour la majorité des applications, un capteur à lames est généralement choisi. Il s'agit d'une technologie éprouvée, dont le cycle de vie et la résistance aux vibrations sont suffisamment longs pour répondre aux applications courantes. Toutefois, d'autres critères doivent être pris en compte pour les demandes spéciales :
- L'environnement : Le cylindre sera-t-il exposé à de grandes quantités de vibrations ou de chocs ? Si c'est le cas, un capteur à semi-conducteurs fonctionnera de manière fiable sans perturbation de la sortie. Les capteurs à semi-conducteurs les plus courants sont les capteurs à effet Hall, AMR et GMR. En outre, le capteur sera-t-il placé dans un environnement clos et propre ou nécessitera-t-il un boîtier à haute protection, comme IP67 ? Les considérations de température doivent également être prises en compte.
- Vitesse de commutation : Quelle est l'importance de la vitesse de commutation de sortie pour votre application ? Les capteurs à semi-conducteurs offrent un temps de commutation plus rapide. Les capteurs à semi-conducteurs les plus courants sont les capteurs à effet Hall, AMR et GMR.
-
Type de sortie : Quel type de signal de sortie le système de contrôle doit-il fournir ? Les signaux de sortie PNP et NPN sont disponibles pour les dispositifs à semi-conducteurs.
- PNP : Une sortie PNP permet d'alimenter la sortie en énergie positive. C'est ce que l'on appelle communément la "recherche de capteurs". La PNP est considérée comme plus fréquente en Amérique du Nord et en Europe.
- NPN : Une sortie NPN permet de relier l'alimentation à la terre. C'est ce que l'on appelle communément un "capteur qui coule". Le NPN est considéré comme plus populaire en Asie.
- Caractéristiques du signal de commutation : Quelles sont les exigences du système de contrôle en matière de puissance de commutation et de courant ? Le capteur sélectionné doit être compatible pour fonctionner correctement.
- Montage : Quelles sont les options de montage disponibles pour chaque type de cylindre ? Selon que vous avez un cylindre profilé avec des rainures ou des tirants ou que vous avez un cylindre rond, les types de montage changent.
- Orientation de l'aimant : Les interrupteurs Reed et les capteurs à effet Hall nécessitent une orientation correcte du champ magnétique appliqué pour fonctionner correctement. Par conséquent, le capteur doit être monté dans le bon sens par rapport au piston.
- Protection des circuits : Si nécessaire, les capteurs peuvent intégrer des protections de circuit, comme les courts-circuits, l'inversion de polarité et la protection contre les surtensions.
- Câblage : Le câblage de l'alimentation du capteur diffère selon qu'il s'agit d'un capteur à semi-conducteurs (AMR, GMR, effet Hall) ou d'un capteur à lames. Un voyant indiquant que le câblage est correct est souvent disponible pour chaque capteur. Par exemple, si la polarité de l'alimentation d'un interrupteur à lames est inversée, la LED du capteur ne s'allumera pas. Les détecteurs à interrupteur Reed ont généralement une configuration à 2 fils, tandis que les détecteurs à semi-conducteurs ont 3 fils. En plus des fils positif et négatif, un troisième fil sera utilisé pour la connexion à la charge. Le câblage correct du fil de charge doit toujours être vérifié avant de mettre l'appareil sous tension, car un mauvais câblage peut endommager le capteur de façon permanente.
Comparaison des capteurs de vérins pneumatiques
Interrupteur à lames | Effet Hall | AMR | GMR | |
Taille | Grandes dimensions | Petit | Moyen | Petit |
Construction | Mécanique | État solide | État solide | État solide |
Force de l'aimant requise | Moyen | Haut | Faible | Faible |
Sensibilité | Moyen | Faible | Haut | Haut |
Stabilité de la température | Moyen | Faible | Moyen | Haut |
Consommation électrique | Zéro | Faible | Haut | Faible |
Immunité au bruit | Haut | Faible | Haut | Haut |
Vitesse de commutation | Faible | Haut | Haut | Haut |
Robustesse mécanique | Faible | Moyen | Haut | Haut |
Robustesse électrique | Faible | Faible | Haut | Haut |
Points de commutation doubles | Oui | Possible | Non | Non |
Lisez notre article sur les vérins pneumatiques pour plus d'informations sur le fonctionnement et les types de vérins pneumatiques.